Germanium coatings are critical for enhancing the performance and durability of optical components made from germanium, especially those used in infrared applications. Here’s a more detailed explanation of the types of coatings used, the coating processes, and the properties these coatings impart to germanium optics:

Types of Germanium Coatings
- Anti-Reflective (AR) Coatings: The primary purpose of AR coatings is to reduce the reflection of infrared light at the surface of germanium lenses or windows. This is crucial because germanium has a high refractive index (~4.0), which naturally leads to high reflectance (around 35% per surface without coating). AR coatings can reduce this to below 5%, significantly improving transmission efficiency in the infrared spectrum.
- Hard Carbon Coatings (Diamond-Like Carbon, DLC): For optical components used in harsh environments, a diamond-like carbon coating may be applied. DLC coatings provide a hard, durable surface that is scratch-resistant and protects against environmental elements like dust and moisture.
- Protective Overcoatings: These are applied over the AR coatings to protect them from physical and chemical damage, thereby extending the life of the optical components.
Ge Dome without AR Coating @ 5mm thickness
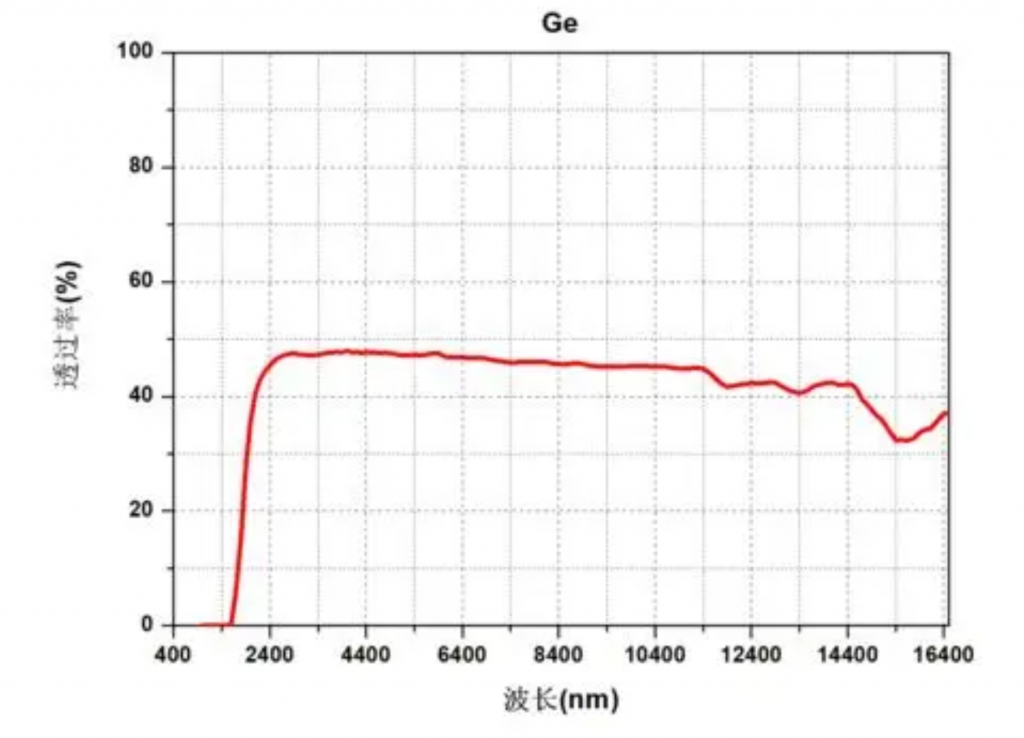
Coating Processes
The process of applying coatings to germanium involves several sophisticated techniques:
- Physical Vapor Deposition (PVD): This method involves vaporizing a solid material into a plasma of atoms or molecules, which are then deposited on the germanium surface. Techniques under PVD include sputtering and evaporation, commonly used for applying thin-film coatings.
- Chemical Vapor Deposition (CVD): For more robust coatings like DLC, CVD is used. In this process, chemical reactions occur at the surface of the germanium when exposed to a vapor of organic compounds, resulting in a thin film of diamond-like carbon.
- Spin Coating: Sometimes used for applying protective polymer layers, spin coating involves depositing a small amount of a solution onto the center of the germanium component and spinning it at high speed to spread the coating material by centrifugal force.
Properties Imparted by Coatings
- Improved Transmission: AR coatings are designed to match the refractive index of germanium to the medium (usually air), reducing reflectance and allowing more infrared light to pass through.
- Enhanced Durability: DLC and other hard coatings protect the germanium from scratches, abrasion, and impacts, which is particularly important for optics used in rugged environments.
- Environmental Resistance: Coatings can also make the surface more resistant to water, oils, and other contaminants, preventing degradation that would otherwise impair optical performance.
SHAPE OPTICS Germanium (Ge) Crystals Specifications
Attribute | Details |
---|---|
Diameter (mm) | 12mm ~ 380mm |
Length (mm) | Customized |
Electrical Resistivity | 0.005Ω ~ 50Ω/cm |
Crystal Structure | Single Crystal, PolyCrystal |
Crystal Purity | 99.999% ~ 99.99999% |
Conduction Type | N/P |
Surface Roughness | Ramax 0.2µm to 4.0µm |
Refractive Index at 10.6µm | 4.0052 |
Absorptance at 10.6µm | ≤0.035 |
These specifications provide key details about the Germanium (Ge) crystals offered by SHAPE OPTICS.
Considerations and Challenges
- Coating Uniformity: Achieving uniform thickness and consistent optical properties across the coated surface is crucial, especially for high-precision optical applications.
- Temperature Effects: Coatings must withstand the operational temperature ranges of the application. Germanium’s temperature-sensitive refractive index can complicate this, as differential expansion between the substrate and the coating may lead to delamination or cracking under extreme conditions.
- Cost and Process Control: The coating processes are high-tech and require precise control, which can be costly. Maintaining quality and consistency in production is essential but challenging.
Overall, the coatings applied to germanium optics are vital for optimizing their performance in infrared applications, extending their usable life, and ensuring they meet the stringent demands of the environments in which they are employed.
Factory Standard
- Germanium Window with different sizes (2 mm – 100 mm)
- Diameter: +0/-0.05 mm
- Thickness: +0.01/-0.03 mm
- Flatness: 1/2 Lambda
- Parallelism: < 3 arc min
- Polished surface finish:20-10 (no dig)
- Bevel: protective bevel
- Transmission rate: >47.5%@3.7-4.8um or according to customer’s specifications
Contact us for manufacturing limit or custom specifications.
Shapeoptics offers a comprehensive range of materials and advanced equipment for custom and OEM optical components, leveraging over 20 years of expertise in manufacturing lenses, prisms, windows, and more. We utilize high-quality materials like UV and IR grade fused silica, Germanium, and ZnSe, among others. Our state-of-the-art techniques and equipment minimize waste and optimize delivery times. Our in-house capabilities include standard and custom coatings across the UV-NIR spectrum, ensuring high quality and compliance with all industry standards. For precision and reliability in optics, contact Shapeoptics for your next project.